**Does your slab sweat?
**Do you have little white puffy clouds on the floor?
**Have you been cited for failure to maintain a safe and slip free atmosphere?
**Ever notice mold and/or mildew forming beneath your carpet or tile…or actually growing directly out of your concrete slab?
**Having a problem getting your flooring to stay in place?
**Was your slab poured prior to 1983?
Click here to read about our floor moisture testing.
In this photo you see evidence of moisture leeching into this door frame. When you trap moisture beneath your floor coverings any trapped moisture will find the path of least resistance in order to escape. This will often include the void spaces in your home like an air vent, in walls, under cabinets and under various floor coverings.
Testing
The flooring industry has multiple methods for testing the moisture content in your slab. Any reading over a 3.0 means that you have some form of moisture working its way from the ground up through your slab. A moisture reading between 3.1-6.0 are relatively common and can be easily handled with proper treatment. A reading of 6.1-12.0 requires a more aggressive approach and readings over 12.0 are considered extreme.
As of the writing of this article readings over 25 pounds of pressure per square foot in a 24-hour period are untreatable with current products available today. Floor moisture can cause multiple problems including floor covering failure, mold, mildew, efflorescence, structural wood rot. It can also cause water damage to furnishings and a host of other issues that can be a financial drain.
Important Note
It is important to note that moisture vapor testing is designed to give you a reading of the current moisture content or the moisture content at the time of testing. There is no current testing method or formula to determine what the moisture content will be a week or a month or a year from the time of testing. If you treat your moisture condition you will likely slow down but not stop the problem.
A few probable causes for slab moisture are:
1. High water tables
2. Broken water pipes within the slab
3. Deteriorated underlayment
4. Weak and/or porous concrete
5. Environmental air pressure
6. Humidity
7. Rain and more.
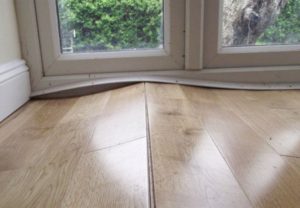
Floor buckling is more common than you might think. Thankfully, this homeowner only had this type of floor covering in one room.
Shown above you see how this newly installed wood flooring has buckled to give way to the pressure of the moisture vapor transmission below.
Efflorescence
In the below picture you will see an extreme case of vapor transmission and the efflorescence it causes. This is more common here in Texas and Louisiana where you will find efflorescence in smaller quantities. Check under rugs, wood flooring, or in storage areas where plastic bins have been stored over a section of the bare floor for a period of time for the telltale signs.
Efflorescence is the result of water rising to the surface in the form of vapor and bringing minerals from the cement with it. As the water evaporates into the air above the slab those minerals are left on the surface and form these “light as air” crystalline mineral clouds.
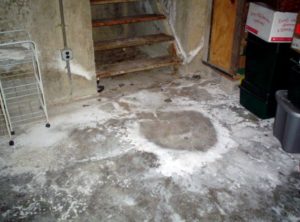
An extreme example of efflorescence on a bare concrete slab.
Here (above) we see efflorescence growing on this bare concrete floor. While this case is rare, a little efflorescence is very common here on the Gulf Coast.
For most cases in the Gulf Coast region this is often a combination of factors and frequently identified in slabs that were built on grade from 1960-1983. During that time frame a tar paper or sometimes a plastic sheeting underlayment was used to block water from under the slab. As time has revealed; this was not a long-lasting solution. Science has now discovered these underlayment types have deteriorated and left the slab vulnerable to capillary action, vapor transmission and other hazards of water transmission. In other cases, contractors did not use any form of underlayment under garages and patios during that time frame. Homeowners have since converted those areas into living spaces only to discover a moisture vapor transmission problem.
Concrete 101
The common misconception is that concrete is a solid surface, however, concrete is very porous and filled with little microscopic tunnels (aka catacombs) similar to a sponge. When the air above the slab is very hot and dry water or water vapor will naturally transmit to the surface seeking dryer air. Equally, when the air above the slab is humid and wet, this same vapor may push down into the surface seeking the dryer soil. This is why pet owners often experience the scent of pet urine long after its first appearance. Vapor transmission will either push or pull the liquid up or down depending on atmospheric conditions.
Pet Smells
Pet urine contains urea, creatine, uric acid, carbohydrates, enzymes, fatty acids, hormones, sodium, potassium, chloride, magnesium, calcium and ammonia. Once introduced onto your slab these compounds could be trapped there for many years. The smell will come back over and over as your slab transmits vapor up or down. This is why removing old, contaminated carpet fails to eliminate pet odors. The cause of the odor is deep within the concrete.
Have No Fear
Have no fear, there are options for remediation of floor moisture. While floor moisture cannot always be permanently stopped it can be drastically reduced in most cases. If you suspect a problem, start with a moisture test to determine your best course of action. At Slip Free Systems we always try to determine if there is a moisture problem prior to your installation. We encourage you to share any suspicions or point out evidence of floor moisture that you are aware of. Concrete floors are tricky in that they sometimes show signs of vapor transmission during a wet season and sometimes not, during a dry spell.
Something you can do right now
A simple do it yourself moisture test that will give you a yes or no answer but not a numerical identifier. Use a piece of heavy plastic sheeting (preferably, but not necessarily clear) about 12-16 inches square and tape all four sides down with duct tape in the center of the room (away from exterior walls). Wait 36 hours. Remove the plastic sheet. If you see moisture on the plastic; or the slab is discolored from damp moisture as compared to the floor around it; then you have moisture transmission coming up through your slab.
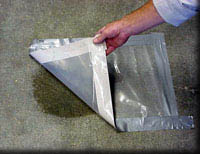
A simple sheet test to determine if there is a problem.
If your DIY test determines that you have moisture vapor transmission it would be advisable to have a professional perform a proper test to determine the amount of moisture in your slab. This will help you make the best choice for your floor coating and/or covering needs.
Expectations
It is VERY IMPORTANT TO NOTE that there is currently no known treatment that can be applied to the top of your slab that will eliminate a moisture problem with 100% effectiveness. The goal of a moisture vapor retarder is to SLOW DOWN the transmission of vapor or to trap it under the vapor retardant. Environmental conditions cannot be predicted. When the temperature above and below your slab are different vapor will transmit either up or down. Ground water tables play a huge role in the amount of vapor and pressure that work their way through your slab at any given time. This is an act of nature and NOT a failure of the products used or the way they were applied.
Wagner Floor Testing Meters has more to say on the subject.
Click here to return to our home page.